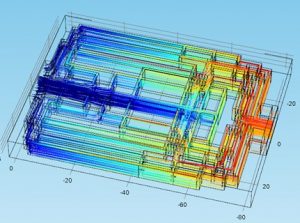
False-colour image of a heatsink genetically designed to cool a module dissipating 2kW
The conclusion comes from two linked projects at Oak Ridge National Laboratory and the University of Tennessee Knoxville:
One proves printed aluminium can at least equal and sometimes better the thermal conductivity of standard heatsink aluminium.
The second has developed genetic algorithms that make use of the freedom of shape available from 3D printing to design heatsinks that fit in the same space as their conventional cousins but work better.
In the thermal conductivity case, a conventional heatsink material (‘6061’, aluminium with <1% Si and 1.5% Mg) was compared with one printed by US firm Linear Mold AMS using an alloy developed for direct metal laser scintering (DMLS) which includes 10% Si and 0.5% Mg, according to ORNL.
At room temperature, the 6061 alloy had a thermal conductivity of 180W/mK, compared to 110W/mK for the printed heatsink – a lower figure here means worse conductivity and therefore a worse heatsink.
At higher temperatures, they both varied in a roughly linear fashion, converging to 170WmK at 220°C.
Heat-treating them both at 300°C, then returning then to room temperature, resulted in structural changes which improved thermal conductivity in both materials.
While the 6061 heatink became a few W/mK better, the printed one was far improved – rising permanently to just under 200W/mK.
For future simulation, the research team has created accurate theoretical models for both the printed alloy and 6061.
As an aside, the most common aluminium alloy for DMLS 3D printing is ‘AlSi10Mg’, which is very similar to the alloy ORNL describes, but with 0.25-0.45% of magnesium.
As printed this achieves 103+/-5W/mK along printed layers and 119+/-5W/mK through printed layers. Standard post-printing conditioning for AlSi10Mg is heating to 300°C for two hours, after which its thermal conductivity rises to 173+/-10W/mK in all directions.
A second standard alloy for extruded heatsinks, called 6063, delivers 190-210W/mK in copper-free form – copper increases thermal resistance in aluminium.
And as a further aside, diamond scores 2,000W/mK in the heatsinking stakes.
Genetic design
With 3D printing capable of making heatsinks just as good as existing heatsinks the same shape, what benefits are available using the arbitrary shapes possible with 3D printing, and how might these arbitrary shapes be designed?
These are questions the second ORNL/Tennessee University project set out to answer, using genetic design algorithms and finite element modelling in COMSOL software.
It took as an example a 50kW water-cooled silicon carbide H-bridge inverter for electric vehicles.
For comparison, a reference model heatsink was created based on a real one from Lytron’s CP15 series, which consists of a thick aluminium plate into the back of which deep grooves are cut. A copper pipe, in good thermal contact with the aluminium, serpentines through these grooves, and water in the pipe carries the heat away.
Two situations were modelled: one with a 64x64mm switching module dissipating 2kW, and a second with four individual power transistors mounted in a square, each dissipating 250W.
Genetic algorithms were used to design 3D-printable same size (~86 x 64 x 8mm) competition for the reference heatsink under both 1kW and 2kW load conditions. In all cases, inlet water at 20°C was assumed to flow into the heatsinks at 0.036 litre/s.
To keep the design algorithms simple, arbitrary water channel shapes were not allowed.
Instead, the channels were restricted to being rectangular in cross section (~6mm tall leaving 1mm top and bottom in the slab thickness, and ~1mm wide).
They had to progress in a rectilinear fashion – that is, they were only permitted to run straight across the heatsink or straight along it.
All corners had to be right angles, T-junctions were allowed, cross-roads were allowed, and two channels touching side-by-side became a 2mm channel – take a look at the top diagram for a better idea.
Calculation was halved by splitting the heatsink long-ways into two symmetrical halves.
Two separate custom genetic algorithms were used to design each printable heatsink – full details are available in a paper: ‘Genetic algorithm design of a 3D printed heat sink’.
Loosely: the first algorithm created “pretty good” heatsinks, according to ORNL, using four iterated steps: initialisation, evaluation-and-selection, crossover-and-mutation, and reproduction.
Initialisation, for example, starts by randomly creating potential heatsinks with a number (anywhere from two to 10) of water channels stretching between the inlet and the outlet. Later steps modify these channels.
After each step in the algorithm, the worst performing ones were discarded.
Scoring for all algorithms was though a badness function: created by adding the temperature of the hottest part of the heatsink (relative to 20°C) to the pumping force required to achieve the fixed water flow – so high scores meant hot components or heavy pumping.
This first algorithm converged rapidly: with a 58°C point on one first-iteration heatsink, dropping to 51.8°C on iteration three, then gradually levelling out to 46°C by iteration 19.
The second algorithm, applied after the first had finished its work, nudged the previously optimised geometries around. Its steps were: translation, connection, creation, and deletion.
Translation, for example, might move a channel sideways a little. Connection would select random points in channels and connect them to a nearby channel. Deletion filled in some loops formed by the three other steps.
In the four separate transistor case, iterations of the second stage algorithm created by-pass passages, re-routing some cool inlet water around the first row of transistors to the transistors behind.
Results
Heatsink | Max temp | Max rise over 20°C | Pump force for 0.036 litre/s flow | Weight |
Reference with module | 53.78°C | 33.78°C | 0.56N | 1292g |
Genetic for module (pictured) | 47.92°C | 27.92°C | 0.55N | 852g |
Reference with 4x die | 53.02°C | 33.02°C | 0.56N | 1292g |
Genetic for 4x die | 44.85°C | 24.85°C | 1.3N | 1035g |
The badness function, used throughout, was deliberately skewed to favour cool components at the expense of pumping energy – although there is an option to alter this balance for future designs. This skew is likely to be the reason there is so much difference between the pumping force required by the two printable heatsinks.
Image by ORNL
Sorce Link
0 comments:
Post a Comment